When it comes to surface integrity, equipment longevity, and quality control in engineering and manufacturing environments, understanding and identifying surface pitting is essential. This is especially true for professionals working with or inspecting components using the VT1000 visual testing system. The topic “VT1000 Pitting Photo Examples: A Comprehensive Visual Guide, ??, (In Title Make a Sense)” aims to provide not only visual representations of surface pitting but also a detailed explanation of how the VT1000 identifies such defects and what these signs mean in real-world contexts. This comprehensive visual guide offers valuable insights for engineers, inspectors, and quality control professionals seeking to better interpret pitting signatures with accuracy and consistency.
Introduction to VT1000 and Surface Pitting
The VT1000 is a sophisticated visual testing equipment applied across a number of industries including aerospace, automotive, marine, and manufacturing. It is mainly created for high-resolution evaluation of surfaces, particularly for discovering irregularities including pitting, cracks, corrosion, and other microstructural faults. Surface pitting refers to microscopic, often circular depressions or cavities that occur owing to localized corrosion. Left undetected, pitting may undermine the structural integrity of materials and lead to failure.
This guide—“VT1000 Pitting Photo Examples: A Comprehensive Visual Guide, ??, (In Title Make a Sense)”—is intended to illuminate the different forms of pitting damage that professionals may encounter, using photographic examples to educate and assist in making more accurate assessments.
Understanding What Pitting Looks Like: VT1000 Visual Indicators
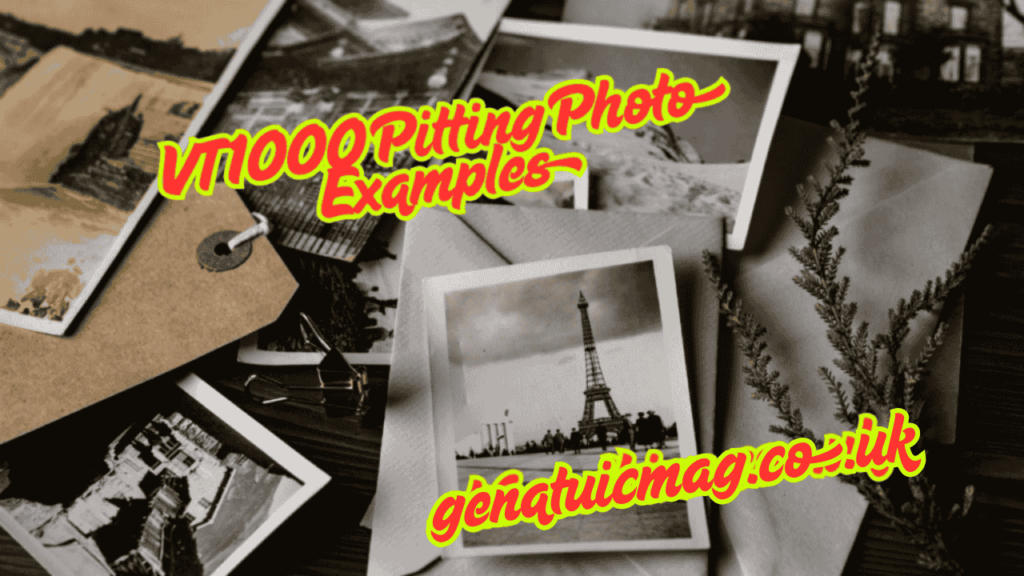
Different Pitting Patterns in Metals
When utilizing the VT1000, pitting appears in various patterns depending on material type, environmental exposure, and surface treatment. Some examples include:
- Uniform Pitting: Regularly spaced pits, often indicative of consistent corrosion exposure.
- Clustered Pitting: Groups of pits in one localized area, typically caused by material impurity or mechanical stress concentration.
- Isolated Pits: Single pits that may represent the early stages of deeper corrosion development.
Each of these patterns is documented through VT1000 pitting photo examples, showing close-up shots that highlight depth, shape, and spread.
Photo Analysis: Mild vs Severe Pittin
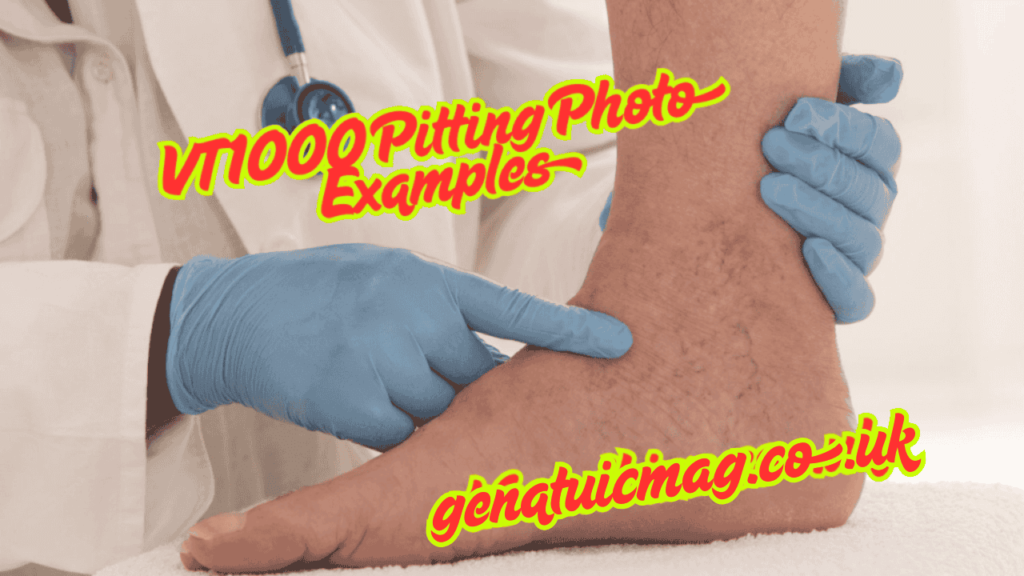
Mild Pitting Examples
In cases of mild pitting, VT1000 photos show tiny indentations barely visible to the naked eye. These may only affect the surface aesthetics and usually do not compromise functionality. However, these minor defects can serve as initiation points for future corrosion if not treated. The VT1000’s optical magnification helps to highlight these early indicators clearly in the photo documentation.
Severe Pitting Examples
Severe pitting, by contrast, is dramatically highlighted in VT1000 pitting photo examples as deep, well-defined cavities that may even have irregular edges. These are often accompanied by signs of rust or material discoloration. The photo clarity provided by the VT1000 allows inspectors to measure pit depth and radius accurately, often correlating these dimensions with allowable tolerance levels in manufacturing specifications.
VT1000 Pitting Photo Examples in Diverse Environments
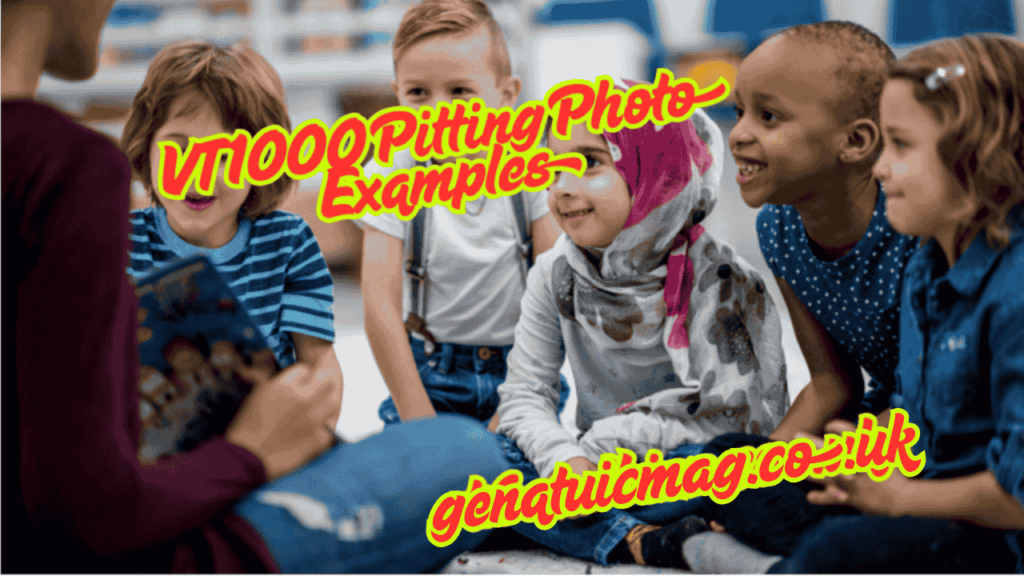
Marine Applications
In marine industries, pitting often occurs due to saltwater corrosion. VT1000 pitting photo examples taken from ship hulls, propellers, and submerged machinery demonstrate how salinity can create widespread pitting. The guide shows photos of early-stage saltwater pitting versus long-term exposure, providing invaluable comparisons.
Aerospace Applications
Aircraft structures require stringent inspection protocols. VT1000 images from aerospace components such as fuselage panels and turbine blades highlight pitting caused by environmental exposure at high altitudes, extreme temperatures, and mechanical fatigue. In the VT1000 pitting photo examples, technicians can examine how pitting begins near fasteners and expands into micro-cracking.
Interpreting VT1000 Pitting Photo Examples for Maintenance Decisions
Decision-Making Based on Photo Evidence
By analyzing the VT1000 pitting photo examples, maintenance engineers can make informed decisions about whether a component can be reused, repaired, or must be replaced. Photo-based documentation from the VT1000 helps create a historical record, allowing comparisons over time to monitor the progress or remediation of pitting.
These high-resolution visuals not only improve internal quality assessments but also serve as evidence in regulatory audits and inspections, especially in industries governed by strict safety standards like aerospace and nuclear power.
Comparative Visual Analysis: VT1000 vs Traditional Inspection
A crucial part of this comprehensive visual guide is comparing VT1000 photos to traditional inspection methods. Conventional methods often rely on the naked eye or simple magnifiers, which may miss early signs of pitting. VT1000 pitting photo examples show a stark contrast in visibility and detail:
- Traditional: May miss subsurface cracks developing beneath pits.
- VT1000: Reveals texture, shape, and microfractures surrounding pits.
This comparative analysis in visual form underscores why many industries have shifted to VT1000-based pitting assessments.
Common Materials and VT1000 Pitting Characteristics
Stainless Steel
Stainless steel is corrosion-resistant but not immune to pitting, especially in chloride-rich environments. VT1000 pitting photo examples show stainless surfaces with pinpoint perforations or orange rust spots that indicate oxidization around pits.
Aluminum
Lightweight but reactive, aluminum shows pitting as white-oxide corrosion marks. The VT1000 captures these distinct patterns, which often differ significantly from how pitting presents in ferrous metals.
Copper Alloys
In copper or brass components, pitting shows greenish discoloration. The VT1000’s high-definition imagery allows inspectors to isolate pitting from general tarnish, a critical distinction in quality control.
Preventive Insights from VT1000 Pitting Photo Examples
This guide isn’t just about identifying damage—it’s also about preventing it. By closely studying the VT1000 pitting photo examples, inspectors and engineers can reverse-engineer the causes of the damage. This could include:
- Improper storage
- Chemical exposure
- Inadequate protective coatings
- Mechanical stress points
The VT1000 offers photographic clarity that makes trend identification and corrective action planning much more efficient.
VT1000 Pitting Photo Examples: A Tool for Training and Standards Compliance
Visual inspection training is another key use of the VT1000 pitting photo examples. These high-resolution photos serve as educational references in technical certification programs, ensuring that all personnel can identify and interpret pitting consistently. Moreover, these visual examples help in aligning with international standards such as:
- ISO 8501
- ASTM G46
- NACE RP0775
In regulated industries, having a reliable visual guide is essential for compliance, and this comprehensive guide supports that need.
Conclusion: The Importance of a Visual Standard
In closing, “VT1000 Pitting Photo Examples: A Comprehensive Visual Guide, ??, (In Title Make a Sense)” is more than just a photographic record—it’s an essential resource for inspection integrity, safety, and performance assurance. By leveraging the VT1000’s capabilities, professionals can elevate their understanding of surface degradation, anticipate failure points, and implement more effective maintenance strategies.
Every image captured, every pit documented, and every comparison made contributes to a safer, more reliable industrial future.
Also Read : VT1000 Pitting Photo Examples: A Comprehensive Visual Guide